Co-operation boosts circular economy in construction
There are many opportunities in the construction industry to promote circular economy and low carbon activities. Construction industry actors of the 3C cluster in Southwest Finland gathered to present new products and ongoing development projects at a seminar in Pargas on 20 September 2022. The event was hosted by Turku Science Park and Nordkalk.
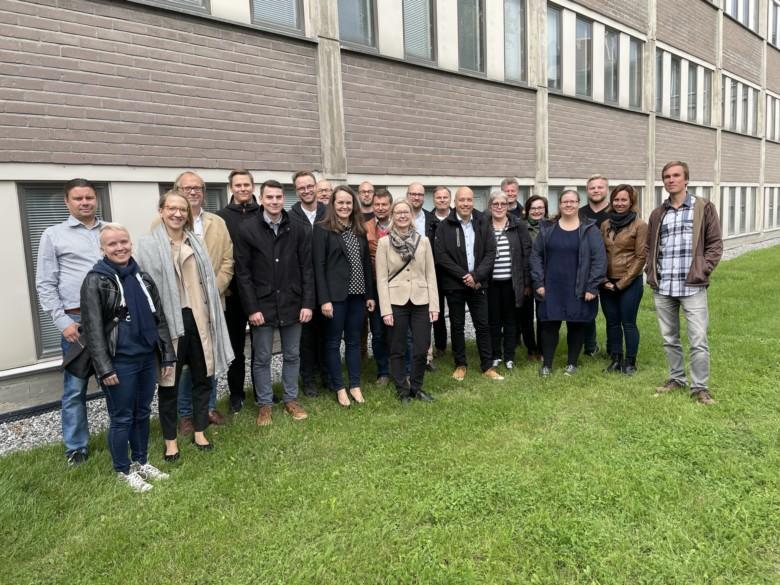
“Have you read my email describing the qualities of our filter slabs”, asks Ismo Kuokkanen, Department Manager, Process R&D at Paroc Group. Ursula Kääntee, Head of Sustainable Development at Finnsementti Oy, replies: yes, she has read the email in which filter plate waste is offered to the cement producer for utilisation, but “the high energy intensity of the plates sounds too good to be true”.
Ursula Kääntee is constantly looking for circular raw materials that are suitable for cement production. The material must meet the quality requirements and function both as alternative raw material and alternative fuel in the coprocessing system of the clinker kiln. For example, tire grit and used roofing felt fit the description and enable Finnsementti to reduce its carbon footprint.
The filter slab waste offered by Paroc, an expert in stone wool products, might well be suitable for Finnsementti’s needs. If so, it would also help Ismo Kuokkanen in his search for solutions to eliminate all waste ending up in a landfill from the plant – a target set for 2025.
This was one of the discussions that took place in the seminar Circular economy and low carbon in the construction industry, organised by the 3C cluster (Circular Materials and Solutions for Construction Industry), the task of which is to promote business operations based on circular economy in construction in the Turku region in Finland. The seminar gathered construction and circular economy experts from companies, institutes of higher education, and from the public sector to share challenges, experiences, and ideas. In the heart of 3C is to pilot the best ideas and eventually develop new circular products, services, and business models.
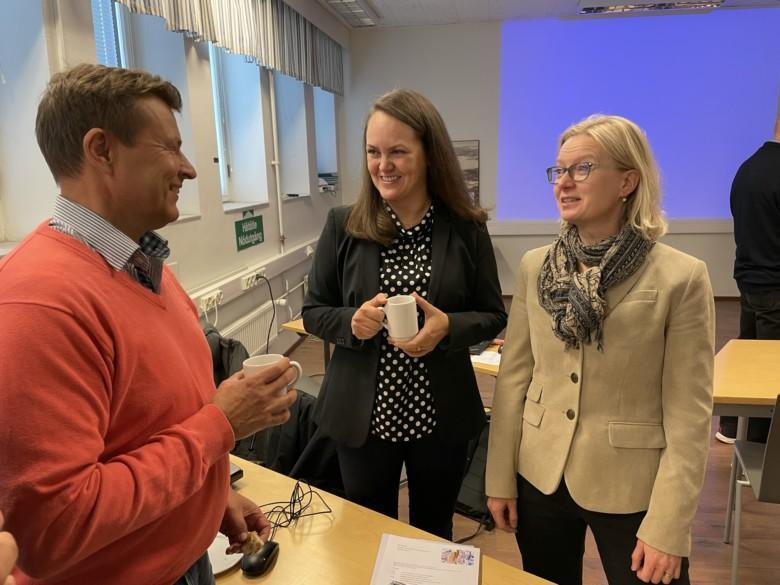
Concrete steps forward
The 3C cluster was founded in 2020, when the pandemic forced networking to take place online. After a string of seven webinars, the seminar in Pargas was the first one where the participants were able to meet in the same room. With 30 people present, the atmosphere was joyful.
“It’s lovely to see people face to face”, summarises Reeta Huhtinen, Network Manager for CleanTurku at Turku Science Park. She is pleased to hear the presentations showing that “circular economy is not just a topic for discussion, but companies are actively developing real solutions.”
Nordkalk’s R&D Director Mathias Snåre agrees: there has been progress both in the 3C cooperation and in product development. At Nordkalk, at least 80 percent of the R&D work concentrates on circular economy. It is a strategic focus area for the limestone company and a part of all customer segments.
One example of a co-operation test within the 3C cluster is the utilisation of Nordkalk’s crushed wall rock in the dry concrete of Saint-Gobain Finland Oy, to replace natural sand.
Finnsementti’s newish CEM III cement, which contains blast furnace slag, received praise at the seminar. It has enabled the Turku-based concrete company Betonilaatta Oy to reduce the carbon footprint of some of its products by 40 percent. Nordkalk has also been using CEM III since this spring, when it replaced traditional cement in the soil stabilisation products.
Paroc has introduced its first carbon neutral insulation slab made of stone wool, PAROC Natura Lana. 15 percent of the stone-based raw material has been replaced by recycled fibres. In addition, low-carbon production technology, the use of green electricity, and partial emission compensation contribute to the carbon neutrality.
Tiileri, which manufactures fireplaces and bricks in Tarvasjoki, has developed a heat stone shell for masonry heaters. 85 percent of the heat stone consists of circular raw material. It is made of waste bricks that have been piling up by the plant for decades – this sight kickstartedthe product development. The current manufacturing process generates practically no waste as everything can be recycled back into the process.
Saint-Gobain Finland Oy coordinates an international innovation project WOOL2LOOP that focuses on the recovery of mineral wool waste from the construction industry. The recycled mineral wool has been successfully ground into low-carbon binding material to be used in concrete-like materials, i.e., geopolymers. This shows that demolition waste can also be used in products with a high degree of processing. The raw material for the project was received, among others, from a demolition site of a health centre in Helsinki, with mineral wool separated from the partition walls of the building.
The KERPUR project (React EAKR), which was started within the 3C cluster, concentrates on the recycling and reuse of ceramic waste. Åbo Akademi, Turku University of Applied Sciences and the Finnish Environment Institute, in co-operation with companies, aim to identify and pilot highly processed products based on ceramic demolition waste. Separate collection of ceramic demolition waste and crushing of ceramics have been successfully tested in the project. There are great opportunities in the recycling of ceramics, because ceramic demolition waste is not yet recycled outside the industry. Ceramic materials are highly processed, energy-intensive materials with possible reuse applications in, for example, ceramics, bricks, asphalt and geopolymers.
“From concrete production to waste treatment”
In circular economy, one’s waste is another’s raw material. Rami Lahti, Managing Director of Betonilaatta Oy, which manufactures products from concrete, jokes that he is actually in charge of a waste treatment plant. Betonilaatta utilises a variety of industrial side streams, such as crushed concrete, blast furnace slag and fly ash.
As a family business, Betonilaatta is always open for testing and cooperation. One of their partners is Renotech Oy, another actor in the 3C cluster. Together, the companies have experimented with geopolymer production.
The biggest challenge in circular economy is financial profitability. Circular solutions are usually started with small production volumes, which often results in a higher per-unit price than that of a traditional product, while customers expect a lower price. Additional challenges include the availability of raw material, quality specifications and related legal concerns, as well as the development of production technologies.
The built environment plays a crucial role in the mitigation of climate change. Low carbon construction is encouraged by law as well: according to the road map put forth by the Finnish Ministry of the Environment, starting from 2025, CO2 emissions will be a consideration when building permits are issued.
Photos and text: Anne Foley